How LSSGB Helps Project Managers Boost Efficiency and Cut Waste
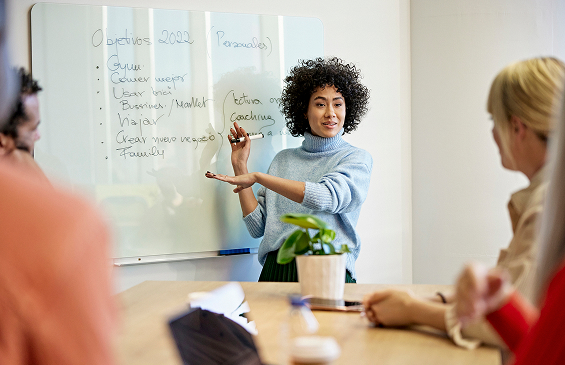
April 29, 2025
What do you do when demonstrations take too long, presentations and materials vary by region, and client feedback is inconsistent? These are the challenges faced by a leading medical devices company before they launched a Lean Six Sigma Green Belt (LSSGB) project focused on optimizing the company’s product demonstration process for a line of medical devices.
Vanessa Brunelli is a Program Advisory Council Member at The Chang School and Project Management Office (PMO) Director, Canada & Latin America for Karl Storz. Drawing from a previous professional experience, she credits the LSSGB approach in the example above with helping her team improve processes and deliver measurable results.
“We achieved a 99 percent compliance in demo kit completeness and presentation quality, a 40 percent improvement in product return service level agreement adherence, a 25 percent increase in post-demo follow-up completion rate, and an increase of customer satisfaction scores by 30 percent,” says Vanessa.
LSSGB is a powerful methodology for driving process improvements and reducing waste, which has a direct impact on project efficiency, cost, quality, and customer satisfaction. These elements determine whether a project manager (PM) is successful or not in an era where organizations are facing increasing pressure to adapt and improve in today’s rapidly changing business landscape.
PMs leading process improvement projects need the skills and tools to drive change, find efficiencies and create sustainable solutions.
Those who use Lean Six Sigma Green Belt (LSSGB) can complement their project management skills by leveraging structured, data-driven approaches to identify root causes, minimize waste, and improve the efficiency and effectiveness of initiatives from planning through execution.
The Chang School now offers the first postgraduate certificate in LSSGB in Canada. Whether they’re looking to grow their knowledge and skills in LSSGB or get a credential for their skill set, pursuing continuing education in this area will help project managers advance their careers and ultimately, the success of the organizations they work for.
What is a Lean Six Sigma Green Belt?
A LSSGB is a professionally trained individual in process improvement methodologies that combine Lean principles (eliminating waste) and Six Sigma tools (reducing variation and defects). Green Belts lead small to medium-sized process improvement projects and assist Black Belts in larger initiatives.
Why it matters to project managers
Project managers like Vanessa care about process improvement and waste reduction because these practices directly impact project efficiency, cost, quality, and customer satisfaction.
How Project Managers Use LSSGB for Process Improvement
Here are some ways that a project manager uses LSSGB for process improvement:
- Identify inefficiencies through process mapping.
- Make data-driven decisions using Define, Measure, Analyze, Improve, Control (DMAIC)
- Apply Lean tools like 5S, Kanban, and Kaizen to reduce waste.
- Monitor performance and apply corrective actions.
In the example mentioned earlier, Vanessa used the DMAIC Approach to address the situation. She shared what that looked like in action:
- Define: We mapped the current end-to-end process using Suppliers, Inputs, Process, Outputs, and Customers (SIPOC) and conducted interviews with sales teams, logistics, and clinical staff to identify critical gaps in execution and ownership.
- Measure: Data revealed that the average lead time to schedule a demo was 12 days, and 30 percent of post-demo actions, like return coordination and customer feedback collection, were delayed or missed. We also tracked recurring issues with incomplete kits, non-compliant cleaning standards, and late returns beyond the defined SLA.
- Analyze: Root cause analysis identified a lack of standardized logistics protocols, unclear responsibilities for product readiness and recovery, and insufficient integration between commercial and support functions. It also highlighted misalignment in incentives that sometimes discouraged timely product returns.
- Improve: We introduced a centralized online request process, created pre-configured and quality-checked demo kits, and implemented pre-shipment checklists to ensure readiness in terms of completeness and presentation. A post-demo follow-up checklist was launched to streamline responsibilities, and we developed a dashboard to track demo scheduling, equipment turnaround time, and customer feedback in real time.
- Control: A governance model with monthly performance reviews was established, including KPIs focused on lead time, equipment readiness, return compliance, and customer satisfaction. We also aligned policies and incentives to foster better cross-functional accountability and avoid conflicts of interest.
Becoming Active Problem Solvers
Overall, Green Belt projects empower employees at all levels to become active problem solvers, says Vanessa.
“By equipping them with structured methodologies and giving them ownership of real business challenges, we create a culture where improvement is part of everyday work – not a one-time initiative,” she says. “These projects serve as catalysts for mindset shifts, encouraging curiosity, accountability, and innovation across teams.”
If you’re a project manager looking to apply LSSGB in your industry or gain formal recognition for your skills, continuing education can help you stand out to employers and advance your career.